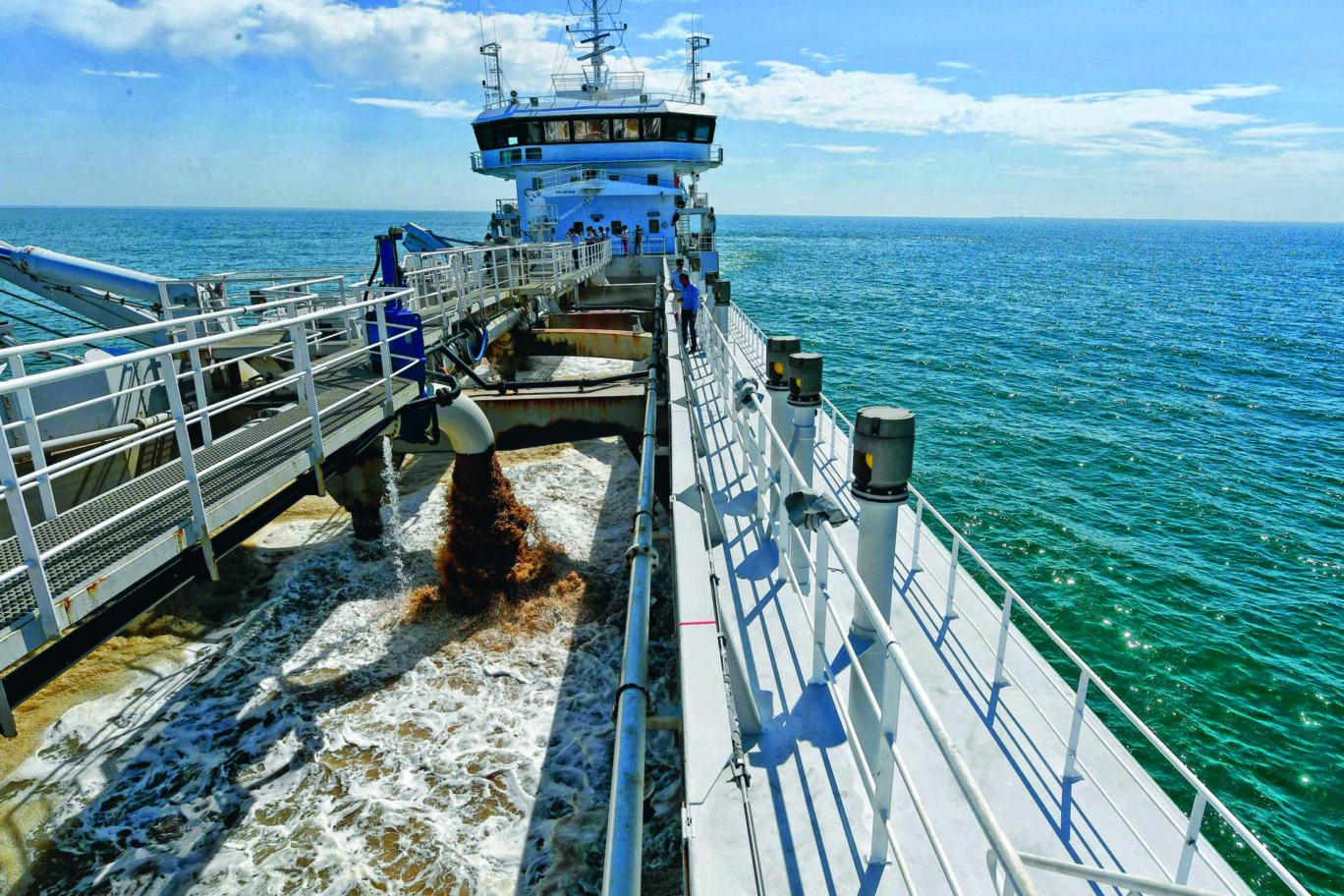
Par Maud Lénée-Corrèze - Comment obtient-on une concession d’exploitation de sable et comment se déroulent les opérations d’extraction sur un sablier moderne ? L’exemple de Stellamaris, un navire de 102 mètres, appartenant à l’entreprise rochelaise Dragages, transports et travaux maritimes (DTM) répond à ces questions, et à quelques autres.
De loin, le Stellamaris ferait penser à un vraquier avec sa grande cale ouverte au milieu… « Il l’est un peu, quand il transporte le sable qu’il a extrait, mais c’est aussi un navire d’extraction de granulats marins, destinés principalement à la fabrication du béton », commente Romain Bernard, ancien capitaine de ce navire sur lequel il a navigué dix ans, et qui est aujourd’hui directeur opérationnel de l’entreprise rochelaise Dragages, transports et travaux maritimes (DTM). Cette société, dont le capital est détenu en majorité par l’entreprise allemande Heidelberg Materials, est l’un des trois principaux armateurs de navires sabliers présents sur la côte atlantique à travailler pour la filière du béton, avec la Compagnie armoricaine de navigation (CAN) et la Société de transport fluvial et maritime de l’Ouest (STFMO). À eux trois, avec leurs quatre navires, ils exploitent la plupart des concessions d’extraction, de l’embouchure de la Manche jusqu’au sud du golfe de Gascogne, déchargeant à Brest, Quimper, Lanester, Montoir, Cheviré, Les Sables-d’Olonne, La Rochelle, Tonnay-Charente, ou Barzan (site des Monards), sur la Gironde. Le secteur du béton, sur cette façade atlantique, est en croissance et consomme 3,5 millions de tonnes de sable marin par an.
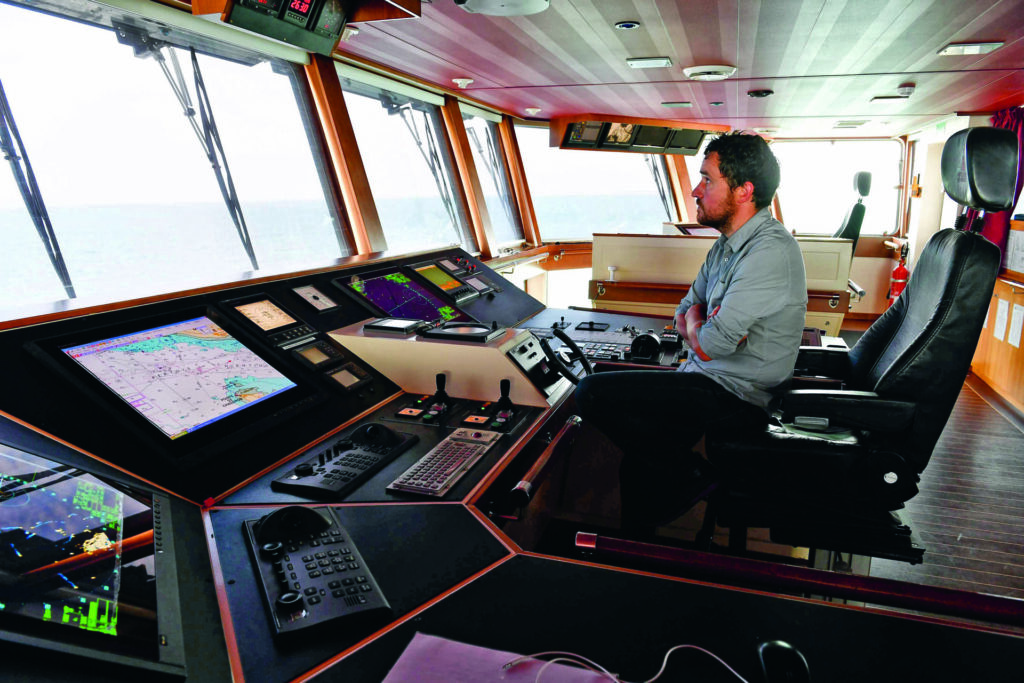
« Le sable que nous extrayons provient de gisements situés sur les lits d’anciennes rivières. On appelle cela du sable roulé, ou alluvionnaire, ajoute Agnès Garçon, directrice Ressources minières à la stfmo. C’est du sable siliceux très qualitatif pour le béton. Il est plus fin que celui que l’on trouve dans la Manche, où il est davantage graveleux. » Ces armateurs ont pour clients les stations sablières dont, souvent, les actionnaires majoritaires maîtrisent tout ou partie de la filière béton. « Ils nous commandent chaque mois un certain tonnage, reflet de la dynamique du secteur de la construction. Nous organisons les rotations des navires en fonction, explique encore Romain Bernard. Sur la côte atlantique, nous travaillons au rythme des marées, soit un nouveau chargement toutes les douze heures, de nuit comme de jour. Sauf en période estivale où pour raisons techniques les bateaux s’arrêtent peu. Certaines concessions sont par ailleurs fermées à des périodes spécifiques de l’année pour respecter les cycles biologiques des espèces benthiques ou halieutiques. »
Plusieurs études d'impacts sont nécessaires avant d'obtenir une autorisation
Car l’activité n’est pas sans effet sur l’environnement. Pour atténuer et limiter ses potentiels impacts, elle est régulée par le code minier français. Une concession portant sur une ou quelques dizaines d’années est octroyée après un long processus qui commence par l’obtention d’un permis exclusif de recherche (PER). « Il impose une première étude d’impact, explique Agnès Garçon, qui permet d’obtenir une autorisation pour des campagnes scientifiques avec études géophysiques (bathymétrie, nature des fonds par sonar latéral), campagne halieutique, benthique, essais de navires pour étudier le panache turbide. » Une fois ce permis obtenu, l’armateur a cinq ans pour construire une autre étude d’impact environnemental, beaucoup plus importante, cette fois pour l’exploitation, « ce qui prend souvent au moins deux bonnes années, ajoute Agnès Garçon. Nous travaillons avec des bureaux d’études qui concentrent leurs recherches sur les communautés benthiques, ce que nous modifions le plus. »
Le code minier, ainsi que plusieurs textes, tels les documents stratégiques de façade, listent les différents milieux, espèces et zones sensibles sur lesquels orienter ces études pour trouver la zone la plus favorable. Si l’extraction est autorisée sur les zones Natura 2000, qui protègent un habitat ou une espèce en particulier, cette étude d’impact devra prouver que l’activité ne les perturbera pas.
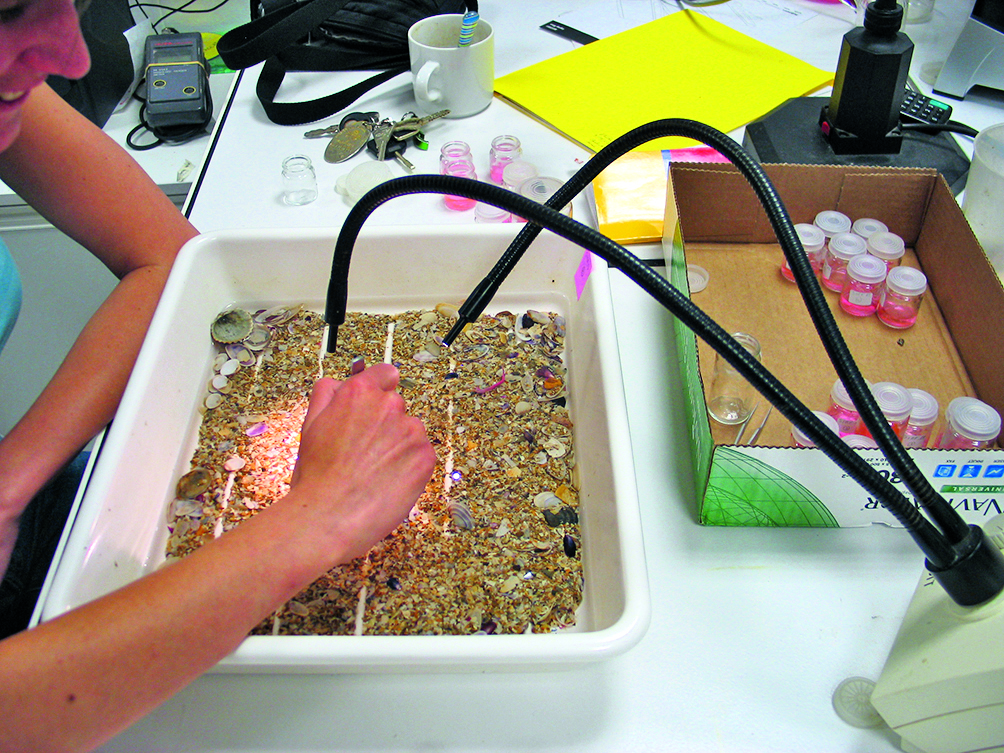
Bien sûr, le PER est aussi l’occasion d’étudier la qualité et la propreté du gisement. Il permet de décrire le milieu pour définir la zone la plus propice à l’extraction, afin de limiter les effets et d’éviter par la suite la plupart des contraintes liées à la préservation du milieu – arrêt pour raisons biologiques, par exemple –, mais aussi de savoir exactement où extraire le sable recherché par les clients. « Ce sont des études très coûteuses, ce qui explique que nous les mutualisons parfois avec d’autres armateurs, sous la forme, par exemple, d’un groupement d’intérêt économique qui détient alors les autorisations, précise Agnès Garçon. Mais un per ne mène pas automatiquement à une autorisation d’exploiter… »
Si celle-ci est obtenue, elle concerne une zone donnée, avec un volume maximum pour toute la durée de l’extraction : pour la zone de Cairnstrath A, par exemple, au large de Noirmoutier, que DTM exploite depuis 2017, les navires ne pourront pas extraire plus de 900 000 mètres cubes annuellement sur vingt ans et sur une surface de 3,6 kilomètres carrés. « À bord, on parle en mètres cubes ; à terre, ça devient des tonnes », précise Romain Bernard. Le Stellamaris, dernier-né de la flotte sablière française lancé en 2012, peut charger jusqu’à 2 800 mètres cubes de sable en une marée sablière.
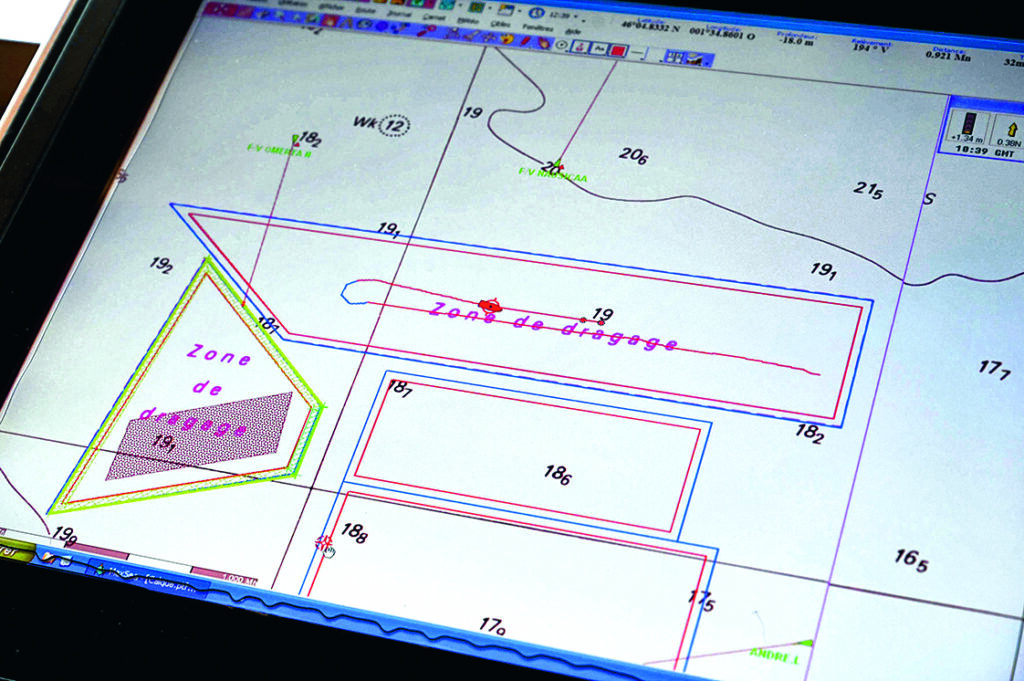
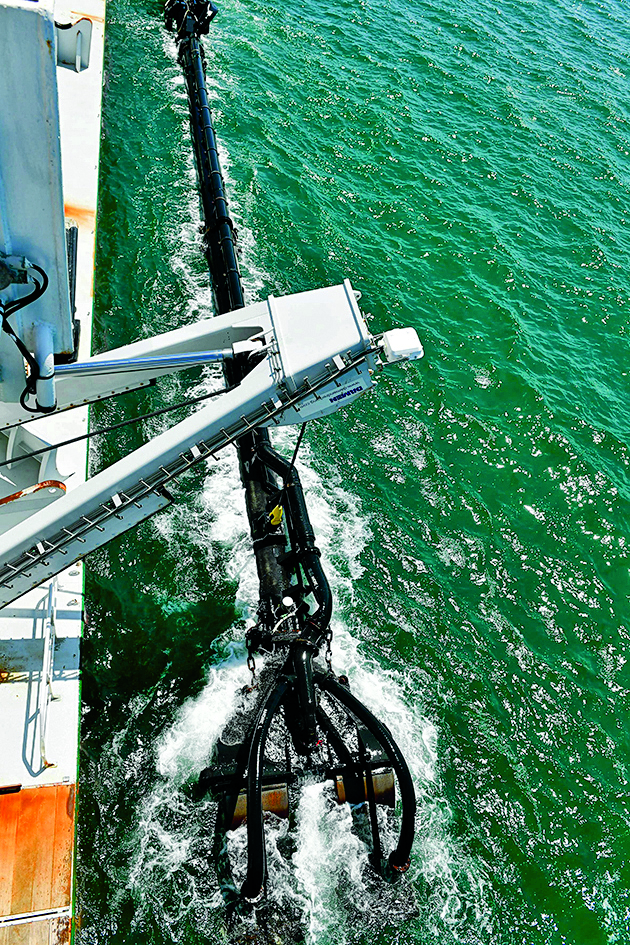
Durant la visite du navire, Romain désigne un gros tuyau de 60 mètres de long posé sur le pont à tribord, à l’extérieur du garde-corps. « C’est l’élinde, l’outil d’extraction. Elle est dotée d’un bec à une extrémité, et d’une ouverture, la plaque d’élinde, à l’autre. » Une fois le bateau sur zone, l’élinde est connectée via sa plaque au réseau du navire, par une ouverture située sur la muraille tribord, vers l’avant. C’est par là que pénètre le mélange de sable et d’eau, aspiré à l’aide d’une pompe de 600 kilowatts installée sur l’élinde. Le Stellamaris, le plus grand navire sablier de la côte atlantique avec ses 102,73 mètres de long et 15,50 mètres de large, peut travailler jusqu’à 45 mètres de fond, même si Cairnstrath, le gisement le plus profond qu’il exploite actuellement, se situe autour de 33 mètres.
Un retour à la mer de l'eau par le fond du bateau qui limite le panache turbide
Le bec qui termine l’élinde peut prélever les sédiments sur une hauteur de 30 centimètres, une grille fixée sur ses deux flaps permettant d’éviter aux plus gros cailloux de s’y introduire. « On travaille la zone de façon à uniformiser les prélèvements pour ne pas se retrouver avec des endroits plus dragués que d’autres », précise le directeur opérationnel.
Lorsque le mélange eau et sable arrive à bord, des capteurs de vitesse et de densité renseignent les marins sur le prélèvement. « Il circule ensuite par ici », ajoute Romain en montrant un tuyau qui traverse le pont dans l’axe du navire, au-dessus de la grande cale. Au fond de celle-ci, quatre réservoirs en forme d’entonnoir, les trémies, communiquent les uns avec les autres. Le sable se tasse dans le fond en losange de chaque trémie, se séparant de l’eau, évacuée à la fin de l’opération par deux goulottes verticales réglables en hauteur, situées dans deux réservoirs. « Ce retour à la mer par le fond du bateau, avec une quantité limitée de sédiments en suspension, provoque un panache turbide moins important que lorsqu’on la vidait par les bords. »
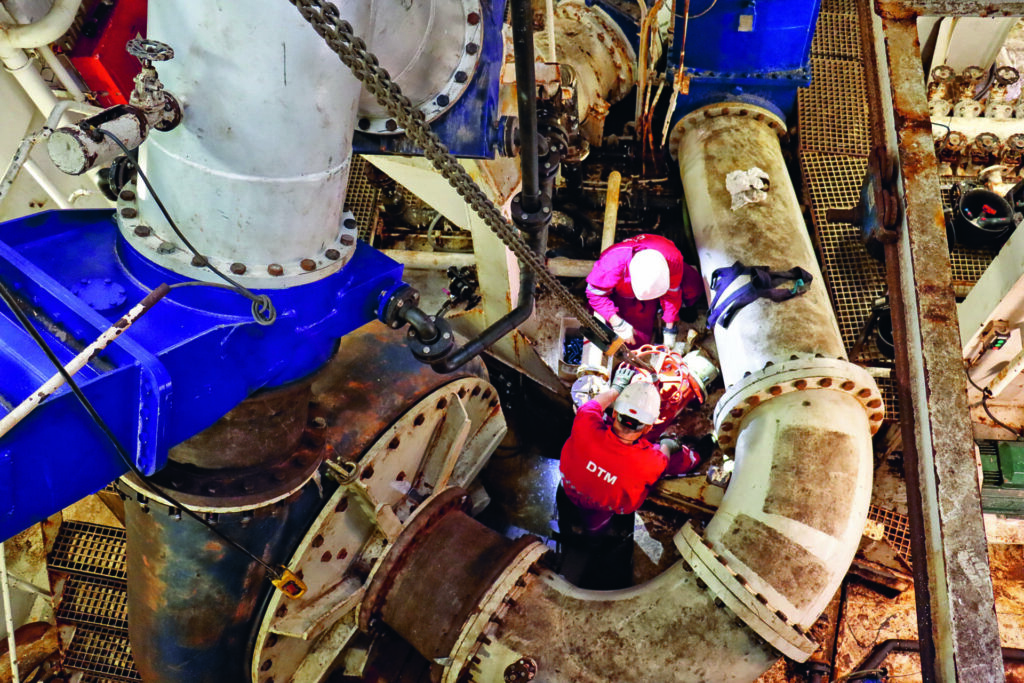
Outre la disparition locale des communautés vivant dans et sur le sédiment par le creusement d’une souille, le panache turbide est l’un des problèmes de cette activité. « Au cours des années d’extraction, nous sommes tenus de faire des suivis environnementaux – menés par des cabinets extérieurs, en lien avec les scientifiques de l’Ifremer – pour évaluer la résilience des milieux et la recolonisation par les espèces », précise Agnès Garçon. Des suivis réglementaires réguliers sont mis en place dans le cadre des autorisations : ils sont d’ordre géophysique, morpho-sédimentaire, benthique, voire même socio-économique quand il existe un conflit d’usage avec les pêcheurs par exemple.
Pendant le chargement, le navire progresse entre 1,5 et 2 nœuds, sous pilote automatique, traînant son élinde, en ligne droite sur toute la longueur de la concession. Deux marins sont de surveillance à la passerelle. Pour le reste, l’innovation et l’automatisation réduit de plus en plus l’intervention humaine. À bord des sabliers de DTM, on compte sept navigants : un capitaine, un chef mécanicien, un second capitaine, un officier polyvalent, un ouvrier mécanicien, un bosco et un matelot cuisinier, qui travaillent sur le rythme d’une semaine à bord, la suivante en repos. Ils font des quarts, surtout la nuit, en huit-douze.
2800 mètres cubes de sable embarqués
« Nous disposons de beaux emménagements, avec une cabine individuelle équipée de toutes les commodités », souligne Romain Bernard, tandis que nous passons devant la cuisine où le matelot prépare le déjeuner. Dans le carré, la table ronde est dressée pour sept personnes. « Tout le monde mange au même endroit, en même temps, à 12 heures et 19 heures, sauf pour l’officier polyvalent qui assure une veille seul au moment des repas. » Un espace équipé d’une télévision et de canapés jouxte le carré. « Et l’été, on peut manger à l’extérieur sur le Stellamaris », apprécie Romain. Pour se dépenser, les marins peuvent se rendre dans la cabine vouée au sport où trônent banc de musculation et vélo d’intérieur.
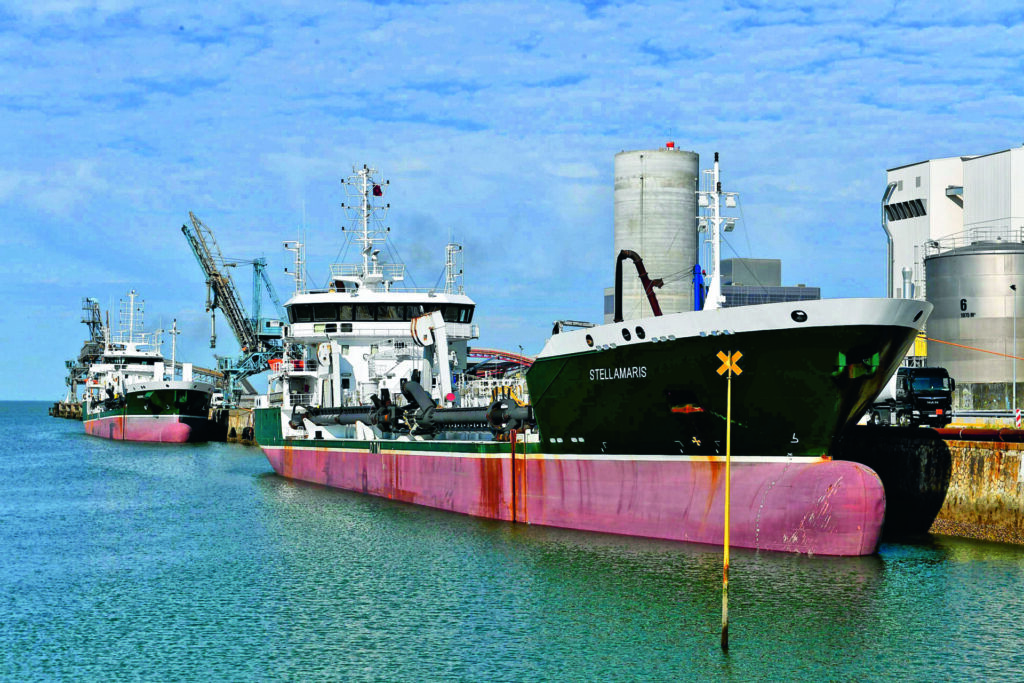
Outre le Stellamaris, DTM a un second navire, l’André L., lancé en 2005, qui mesure 84,85 mètres sur 15,20 mètres de large et qui peut charger 2 200 mètres cubes. Tous les deux sont armés de la même façon, ce qui facilite leur entretien. Les trente-cinq marins de l’armement tournent sur les deux navires, sauf les chefs mécaniciens pour des raisons de suivi du bateau, et les capitaines qui détiennent aussi une licence de pilote.
Revenons en mer, au moment où le chargement s’achève, au terme de deux à trois heures de navigation. Les 2 800 mètres cubes de sable sont embarqués et ont décanté. L’eau est repartie à la mer, l’élinde est remontée et le navire fait route vers le terminal sablier le plus proche, souvent situé à moins de six heures de navigation pour être certain d’arriver à marée haute, le tirant d’eau du navire étant de près de 7 mètres en charge. Une fois à quai, on branche la pipe de déchargement du terminal à une sortie située au centre du pont, raccordement qu’on peut réaliser depuis la passerelle. « Ici, sur la côte atlantique, nous ne faisons que des déchargements hydrauliques, explique Romain Bernard. C’est sans doute historique, et lié à la nature du sable, plutôt fin. Plus au nord, les déchargements se font principalement à sec, sur des tapis roulants. »
Le métier s’apprend en embarquant en doublure avec un officier formé
Pour ce faire, depuis l’arrière, on pompe de l’eau qui va circuler vers l’avant en se mêlant au sable de la cale. Arrivé aux deux tiers du navire, le tuyau contenant ce mélange se raccorde à une pompe qui va le propulser à terre. « On décharge rarement bord à quai, mais plutôt sur un terrain concédé par le port, parfois distant de 600 à 700 mètres du bateau, ajoute Romain Bernard. C’est pour ça que notre pompe de déchargement de 1 500 kilowatts est beaucoup plus puissante que la pompe de chargement. » Elles sont toutes les deux entraînées par des moteurs électriques alimentés par un Diesel principal de 4 000 kilowatts. « Les moteurs électriques sont isolés dans un compartiment à l’avant du local pompe, afin de ne pas être endommagés si un tuyau contenant du sable et de l’eau fuyait. »
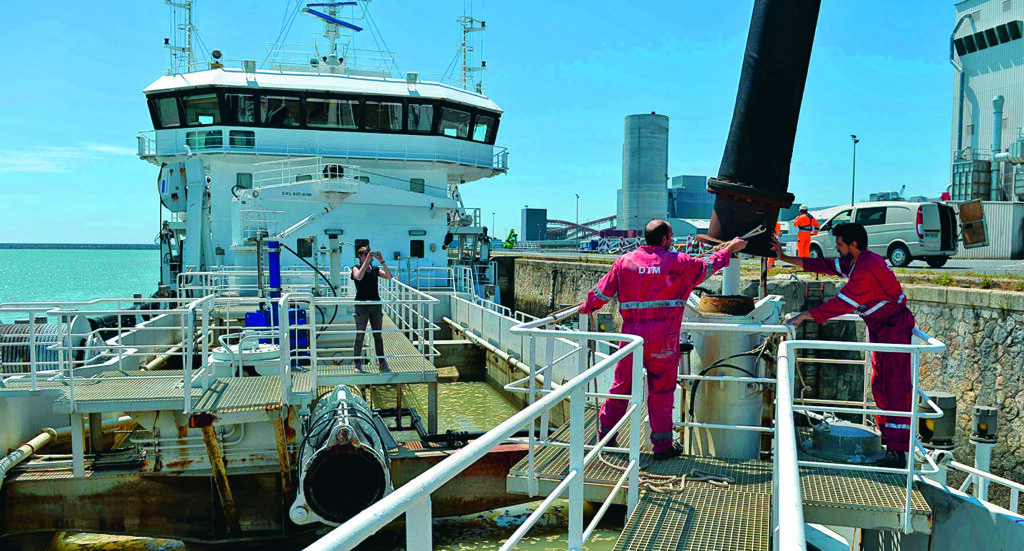
L’opération de déchargement dure entre une heure et une heure et demie. Une fois la cale vide, le navire repart en mer. Les marins ne connaîtront la qualité exacte du sable extrait que vingt-quatre heures après son débarquement, une fois qu’il aura décanté et qu’il aura été analysé par le terminal sablier. « Cela dit, comme nous connaissons bien nos concessions, et qu’avec l’expérience, le marin peut déduire la nature du sable grâce aux données de vitesse et de densité du flux, nous savons presque en direct ce que nous allons livrer. »
Pour exercer ce métier spécifique de la marine marchande, il n’existe pas de formation particulière. Les marins sortent pour la plupart de l’École nationale supérieure maritime ou viennent du milieu de la pêche. Les officiers apprennent la spécificité du dragage en embarquant en doublure avec les officiers déjà formés. Le rôle du capitaine est déterminant : le temps de chargement, une donnée commerciale cruciale, est certes lié à la vitesse d’aspiration, la météo, la profondeur et le type de sable, mais « aussi au marin », insiste Romain Bernard. Et c’est le commandant qui prend la décision finale de se risquer en mer ou pas, en cas de gros temps. « Notre limite, c’est 3 mètres de houle, pour des raisons techniques. En-dessous, c’est à l’appréciation du capitaine. » Le Stellamaris dispose en effet d’un compensateur de houle qui garde en permanence le bec de l’élinde bien collé au sol. « Quand la houle est longue, on peut facilement aller jusqu’à 3 mètres, mais si elle est courte et qu’il y a du vent, il arrive qu’on ne puisse pas travailler au-delà de 2,50 mètres de creux. »
Mi-septembre, le Stellamaris a rejoint la Manche pour une longue campagne, avec relève à Honfleur. Quand il n’extrait pas du sable, le navire peut aussi effectuer ponctuellement du dragage pour l’entretien du port de Lanester, où il pompe un mélange de vase et d’eau qu’il déverse au large sur une zone de dépôt de déblais. « C’est anecdotique comme activité, précise le directeur opérationnel de DTM. Nous pourrions aussi à l’avenir effectuer du dragage pour du rechargement de plage, car lors de la conception du navire, nous avons ajouté un tuyau qui permet d’éjecter du sable par l’avant. »
Avec la montée des eaux, cette branche du secteur de l’extraction de sable marin prend en effet de l’ampleur, en particulier en Belgique et aux Pays-Bas. Les techniques restent les mêmes, même si les réglementations et les processus peuvent différer. En attendant, Sébastien, le matelot cuisinier vient de terminer la préparation du repas, et les marins sont invités à passer à table, avant de repartir en mer. ◼